Innovation Cultures – Modern Methods of Construction and the one barrier that rules them all…
SWPA have been working with Bristol Housing Festival for several years, most recently we have partnered together with Constructing Modern Methods to create our latest procurement solution – the Low Carbon Offsite Housing Construction DPS.
Jez Sweetland, Project Director at Bristol Housing Festival has been exploring innovation cultures in Modern Methods of Construction (MMC), read all about it and see the Top 10 Tips!
In August 2021 Trowers and Hamlins reported on its latest survey of modular housing in the UK. Interestingly some of the original ‘barriers to engagement’ they survey identified in 2019 with MMC (design quality, lack of standardisation and inadequate insurance) have been somewhat addressed as the supply chain has matured and finance – for the affordable housing sector - has to some extent been unlocked through Homes England’s strategic focus.
Trowers and Hamlins 2021 survey lists ‘concern about future maintenance of the homes’, ‘lack of familiarity with process of delivering MMC projects’ and ‘lack of knowledge of availability and ‘types of MMC products’ as some of the primary barriers to engagement as organisations are ‘still waiting for the test of time and further evidence to demonstrate the longevity of modular housing’. If only there was not a housing crisis, or climate emergency or developing construction skills crisis that might necessitate more urgent action –most succinctly summed up by Mark Farmer as ‘Modernise or Die’ – perhaps even more presentient than he intended in 2016 in light of the escalation in our planet’s warming! Of course, whilst new procurement solutions and digital innovations such as the SWPA’s Low Carbon MMC DPS which works with Constructing Modern Methods are important enablers to help overcome some of those real and practical barriers but there is still the ‘cultural innovation barrier’ to address and for many public bodies or publicly funded bodies that still provides arguably the most significant challenge.
At its heart MMC is still an innovation journey for any organisation as the decision-making processes and sequencing, legal, funding, procurement, project management and ongoing asset management all necessitate a new methodology. To some extent that is akin to shifting from ‘operating as experts’ who understand how to manage risk and adversarially negotiate value to a ‘learning culture’ that relies on healthy collaboration and trust as it is required to work with a new supply chain that is still scaling and maturing.
However, as we shift to a genuine and reliable supply chain of manufactured homes the rewards on offer look genuinely capable of providing a route to constructively diversifying the existing build and capex house building methodology whilst providing a desperately needed additional supply of quality, sustainable, affordable homes at pace with greater cost controls and reduced snagging.
In April 2020, a consortium of partners was awarded an Innovate UK grant for their project Enabling Housing Innovation for Inclusive Growth. This project was led by YTKO and included Bristol City Council, Bristol Housing Festival, BRE, Arcadis, Unit 9, and nine leading modular housing companies – with an intended output of over 450 homes in Bristol. Nationally, Bristol City Council, partnering with the Bristol Housing Festival, is increasingly being seen as a leader in the use of MMC housing solutions, an exemplar for the wider UK.
The project outcomes included an ‘Innovation Enabling Model’ supported by a decision-support 'toolbox', with the ambition in the longer term for these to enable Local Authorities or Public Sector Bodies across the UK to address barriers to engaging with MMC. The project also led to the production of the digital tool Constructing Modern Methods and its partnership with SWPA’s Low Carbon MMC DPS.
The overall aim of the project was to unlock the scale of the MMC marketplace by driving research and development to improve the cost, performance, and speed of MMC building across the nine demonstrator sites and to create an exemplary model for other Local Authorities or Public Sector Bodies to invest in MMC across the UK. Another major opportunity was for this project to consider housing holistically, to not just build units, but to consider the implications in the way homes and communities are built and the knock-on effects of these decisions.
The specific aim of the Innovation Enabling Model was for Bristol to learn how to effectively and efficiently use MMC, while ensuring policy lined up with delivery. The intended process was to use the 9 sites as test cases (demonstrators) through which the council and its partners could evaluate and learn from the practical use of MMC in ‘real-world’ scenarios. In essence to establish that required learning culture and ensure that systems were set up to move into that ‘innovation culture’ with clarity of purpose, vision and with a confidence that lessons would be learnt in a safe environment for the right reasons. The report summarised some its findings to address that cultural innovation barrier by identifying 10 recommendations which are set out below to encourage and challenge others to make that step change. The full report can be read here. In addition the project produced a 2nd report ‘Performance Data and Case Studies’, That report, led by BRE with support from Bristol City Council, Rider Levitt Bucknall and Constructing Excellence, focusses on one of the project’s key objectives: to define ‘key performance indicators’ (KPIs) for MMC and benchmark against existing housing delivery models.
- Be ready to genuinely invest in MMC, be strategic in your engagement with the new technology. MMC is a significant change to the development model and therefore, pilot projects can be very costly in terms of time money and resource making it inefficient to engage with a pilot without a broader strategy and a pipeline.
- Strategically support the development of good values in the MMC supply chain.
Local Authorities and Housing Associations as housing commissioners and/or significant landowners, have a strategic opportunity to support MMC so that the supply chain matures along a good value chain as the new housing supply comes online. - Strategically support the development of the MMC supply chain to increase supply.
MMC is offering an additional housing supply at pace rather than replacing what already exists. By strategically engaging with the MMC supply chain organisations can support upskilling of the workforce through companies whose business model rests on the quick delivery of homes. - Know what you want and be clear in your communication.
There needs to be a clear link between Local Authority policy and political ambition, and the delivery. Ensure there is a strategy to implement the ambition on the ground among officers, communicate clearly internally, ensuring there is a strong narrative to explain the use of MMC and the need for change.
- Utilise a ‘one stop shop’ approach.
We recommend a multi-disciplinary team approach and ensuring high level buy in. The novelty needs to be flushed out within the organisation as timings, governance, and sequencing is different. It is important to ensure cross departmental communication and the sharing of expertise between teams involved. - Recognise that not all value is created equal and know the constraints of your tools (i.e. ProVal).
Cost and value are different things, and it is important to consider the whole-life value proposition, how this can be defined and quantified within a value for money assessment. This will need to be beyond traditionally recognised financial indicators to account for additional economic, social, and environmental benefits and savings. It will also need to more carefully consider the value exchange between increased upfront capex and revenue (whether by way of savings or by income over the life of the housing).
- Be willing to learn and open to change.
It is essential to acknowledge that there will be uncertainty and iteration when working with new technologies and supply chains. Honest articulation about MMC in its current lack of maturity is important and engaging with MMC will require a different risk management culture. In our opinion it is important to find the time to invest staff learning, even though people are stretched as embedding institutional learning is vital.
- Engage with the supply chain as early as possible to understand and influence the design and system application
It is important to recognise that there is a resequencing of decision making when using MMC. Early engagement with suppliers is essential to ensure requirements are met and to drive value. Recognise that MMC is a tool and there are a diverse range of MMC products and systems available but there are tools out there (such as CMM and Place Intelligence) to help navigate the market.
- Collaborate from the beginning.
Collaboration around MMC has the potential to change the culture of the construction industry. Replication, repeat business and scale are vital in leveraging the production efficiencies and economies of scale associated with the manufacture of new homes. This manufacturing approach puts the onus on establishing long-term partnerships and maintaining healthy and effective working relationships. This will include elements such as adopting the appropriate contract as soon as possible to facilitate collaboration and risk sharing. Alliance contracting has emerged as one of the most effective tools in maximising the impact and value of MMC demonstrator schemes.
- Embrace the change.
Nationally we are in an urgent situation. We have a housing shortage, a context of social inequality and brokenness, ongoing destruction of our planet, ecology, and climate emergencies. We are in URGENT need to change the ‘norm’ and defending the status quo is no longer excusable.
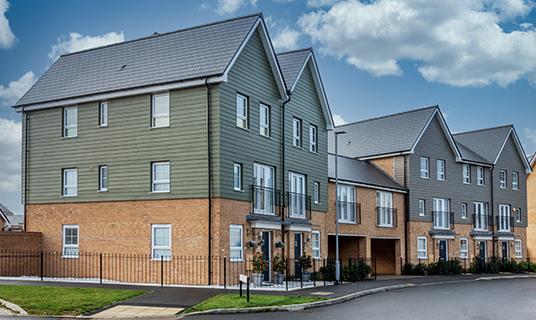